铜红冲及铜合金锻造工艺
铜是具有面心立方晶格的金属,没有同素异形转变,因此它在室温和高温下都具有高的塑性,可以进行冷热压力加工。在锻造生产中,铜质零件品种很多,有纯铜及铜合金(普通黄铜和硅黄铜等),有自由锻件和模锻件,有形状简单或形状很复杂的。在长期的实际生产中,存在着许多不同的质量问题,因锻造裂纹导致工件报废的案例不少。
(一)铜合金锻造的铸锭
铜红冲及铜合金铸锭的宏观组织存在三个明显的结晶区域(图1.5.3)。髓着铸锭浇注温度及冷却速度的不同,铸锭中柱状晶区及等细晶区所古的比例是不同的。对于铜及铜合金来说,当其杂质含量较少时,铸锭具有比较发达的柱状晶区,塑性比较好,而且由于柱状晶组织致密,锻成的锻件质量较高。反之,如果杂质含量较多,柱状晶过分发达,则对锻造是不利的。因柱状晶区过分发达,甚至扩展到铸锭的整个截面,这样就会在柱状晶粒的交接处集中许多杂质和低熔点共晶体,该处成为铸锭的“弱面”。“弱面”的存在,易使铸锭锻造时沿“弱面”开裂(图1.5.4)。大多数铜合金的结晶温度范围较窄,易形成大
图1. 5.3立浇水冷圆形铜锭的低倍组织
图1.5.4黄铜锭锻造时沿纵向“弱面”裂为两半
的集中的缩孔,若冒口设计不合理,缩孔会扩展到铸锭内部,若锻造或挤压时未被切尽,则会在半成品或锻件中留下“残余缩孔”。用普通方法浇注的铸锭,易产生这种缺陷。半连续浇注的铸锭没有形成这种缺陷的危险,因为铸锭的结晶条件好、铸锭很长,缩孔不可能留在铸锭上。
铸锭作为大型锻件的坯料,在锻造前要进行均匀化退火,以改善塑性。铸锭表面若有裂纹、气泡、夹渣、结疤等缺陷应磨干净,或表面经车削(扒皮)后再进行锻造。用于自由锻造的铜合金铸锭,对冶金质量应有更高的要求,有害杂质的含量必须控制在很小的范围内(例如铅含量应不超过0. 01%)。否则,自由锻时由于拉应力的作用,容易在低熔点杂质聚集的地方产生裂纹。铜合金铸锭若作为模锻毛坯,经适当的制坯后可直接进行模锻,而不必像铝、镁合金那样,要经过自由锻反复镦拔后才能用于模锻。因为铜合金的组织不像铝、镁合金那样复杂,塑性也较高。
(二)铜合金热变形温度
铜合金热变形温度如表1.5.5所示。
表1.5.5铜合金热变形温度
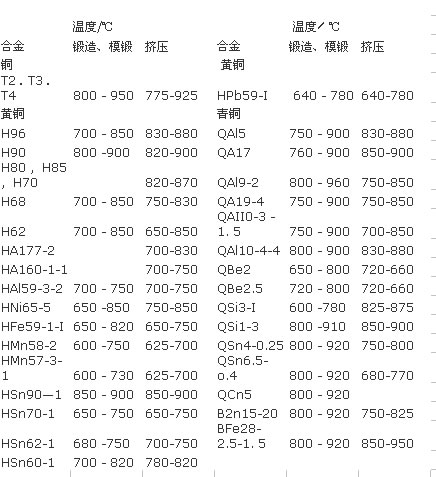
任务实施
一、铜红冲及铜合金锻造工艺
锻造工艺举例:锻件材料为7075合金,锻件重量0. 382kg;毛料规格φ45mm×150mm,毛料重量0.65kg。锻件模锻斜度为外7 °,内10 °,垂直尺寸公差+1.2;-0.7mm,残余毛边每边允许至1.8mm。Ⅲ类件,按A-A取低倍。
工艺过程如下:
(1)下料。采用砂轮切割机下料,车端面,倒圆角R5。
(2)加热。采用电炉加热,炉温(450±10)℃,加热保温时间136min。
(3)模锻。模锻设备为6300kN摩擦压力机,首先在锻模的镦粗台上将坯料压扁至H= 24mm,再在型槽内平放料进行模锻,并压2-3mm。
(4)加热。炉温(450 +10)℃,加热保温时间为30min(第二火)。
(5)模锻。压至尺寸。
(6)加热。炉温(450 +10)℃,加热保温时间为10 - 15min。
(7)热切边。
(8)酸洗。按酸洗通用工艺规程进行。
(9)热处理。按热处理工艺规程进行淬火、人工时效。
(10)锻件修伤。
(11)锻件检验。100%检查材料牌号、外形及表面质量;100%检查硬度(≥40HBS);低倍检查。
二、纯铜的红冲或锻造工艺
以下为某企业纯铜的红冲或锻造工艺缺陷及改进措施举例:在过去的纯铜锻造生产中,曾因锻造裂纹导致大量工件报废。
1.原始情况
工件是材质为T2的圆环类自由锻件,有300多种,外径φ400 - 2265mm,内径φ300 - 2l00mm,厚度20 -125mm。工艺采用铜锭锻拔长条后,弯圈焊接成型。使用设备为燃油加热炉、7. 5kN空气锤和圆弯机。锻造温度为650 - 900℃,实际锻造温度凭经验判断。
2.质量情况
铜锭在7. 5kN锤上拔长时,锻3-5锤时,坯料表面开裂,纵向、横向裂纹都有,但多数为横裂。
3.质量分析
(1)化学成分分析。锻件因裂纹报废共10余吨,每批次都取样检测了化学成分,共取样11次。化学成分(质量分数)中Pb的平均含量超标0.021%、Bi的平均含量超标0. 0128%、Sb的平均含量超标0.0007%,杂质含量均严重超标。
(2)金相分析。
1)少量非金属夹杂物分散分布,颗粒细小。
2)金相组织为α-晶粒,大小不均匀,其平均直径d =0. 1mm,晶粒度相当于11 -12级。
(3)铜锭剥皮后锻造发现仍有裂纹出现。
(4)分析与结论。
1)导致环在锻造时产生裂纹的主要原因是杂质元素(Bi、Pb、Sb等)超标。Bi、Pb、Sb等含量大大超过标准,这对铜的导电性和塑性都有影响,尤其是过量的Pb和Bi在铜中的溶解度很小,它们与铜形成Cu-Pb和Cu-Bi低熔点的共晶体(熔点相应为327℃和270℃),呈网状分布于固溶体的晶界上,削弱了晶粒之间的联系,导致塑性骤然降低而开裂。
2)次要原因是始锻温度控制不严和变形量过大。因为锻造温度是靠操作者凭经验看金属颜色来判断,实际锻造温度很难把握。始锻温度过高时,低熔点共晶体熔化使铜质锻件易于开裂,造成“热脆性”。
3)在始锻时,变形量大,由于热效应,温度的增高也可使低熔点共晶体熔化,破坏晶粒间的结合,导致开裂。
4.改进措施
(1)铜锭改为圆铜棒,加强原材料检查,材料的化学成分必须符合GB 5231-2001的规定。
(2)锻造温度确定为650 - 850qC,锻造温度的测量使用远红外线测温仪。
(3)采用电炉加热。
(4)始锻时,变形程度控制在10% -15%;
(5)锤击应轻快,翻转自如以免热量散失。
5.效果
改进工艺及材料后的锻造生产中,基本消除了锻造裂纹,质量明显提高,合格率达95%以上。
任务总结
铝合金锻造的相关工艺要求及规范制定。镁合金的锻造工艺、钛合金的锻造工艺、铜合金的锻造工艺,结合实际生产确定一种典型合金产品的工艺规范。